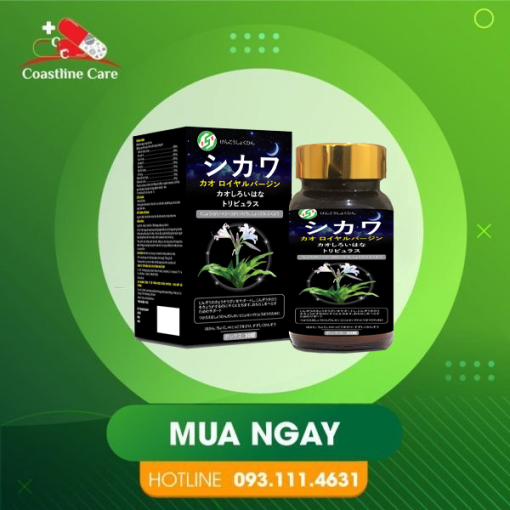
This can be more frequently found in manufacturing processes which could working experience fewer conversation with mother nature or procedures that do not need continuous measuring or refinement.
His instructional background in chemistry laid the inspiration for his analytical method of challenge-solving, which he would later use to high quality management.
P: No matter whether freshly fashioned or taken from an Ishikawa diagram, the hypothesis must make some sort of prediction (or approach
A simple fishbone diagram does not have any predetermined categories. Alternatively, the Group sets forth the groups it items are most beneficial to investigate. They might be elements of Every diagram talked about previously mentioned or totally distinct classes.
The Ishikawa diagram was produced by Kaoru Ishikawa in the course of the 1960s as being a means of measuring top quality Management processes during the shipbuilding industry.
Figure out root triggers: Use five Whys to breakdown Every single from the prioritized causes additional right until you get to the root trigger (course of action breakdown). Take Motion: Use the insights gained to establish solutions or motion strategies to address the root triggers recognized.
Ishikawa diagram, also called the nha thuoc tay Fishbone diagram, is usually a tool used to determine difficulties in a very method. It exhibits how brings about and outcomes are connected and can help assess what is going Incorrect with techniques, processes, and goods. The name comes from Japanese engineer Kaoru Ishikawa who developed the method in the sixties.
Causes of a part not becoming installed may be detailed as sub-branches, even so the precedence should be on figuring out Should the component was set up or not. If a part is not effectively put in, then make use of the 5 Whys on that Portion of the Ishikawa diagram for investigation.
Kaoru Ishikawa’s perform has become instrumental in shaping the sector of quality administration. His enhancement in the Ishikawa Diagram and promotion of high quality circles have supplied powerful tools for pinpointing root leads to of problems and fostering a collaborative method of excellent enhancement.
To break down (in successive levels of depth) root will cause that most likely contribute to a certain nha thuoc tay impact
Analyze the Diagram: Critique the diagram to identify interactions and prioritize leads to for further investigation. It is possible to prioritize working with precise facts, multivoting, nominal group methods, or gaining consensus within the workforce.
Compose the issue assertion with the center-ideal on the flipchart or whiteboard, box it, and draw a horizontal arrow functioning to it.
The 6Ms during the Ishikawa diagram are critical elements accustomed to discover and assess complications in a method. These factors consist of:
Other widespread works by nha thuoc tay using with the Ishikawa diagram involve employing it like a methodology for producing item styles that solve simple complications. It can even be Utilized in excellent defect prevention to determine potential things triggering an All round effect.